Introduction
Aluminum Die Casting is a widely used manufacturing process, producing parts for industries such as automotive, aerospace, and electronics. However, a significant challenge in this process is porosity, which can compromise the structural integrity and performance of aluminum die-cast products. For buyers seeking high-quality Aluminum Die Casting service, understanding how to prevent porosity is critical to ensure reliable and durable components.
In this article, we will explore the top techniques to minimize porosity in Aluminum Die Casting. These methods can help businesses find the right Die Casting factory that adheres to best practices, ensuring the production of superior, low-porosity products.
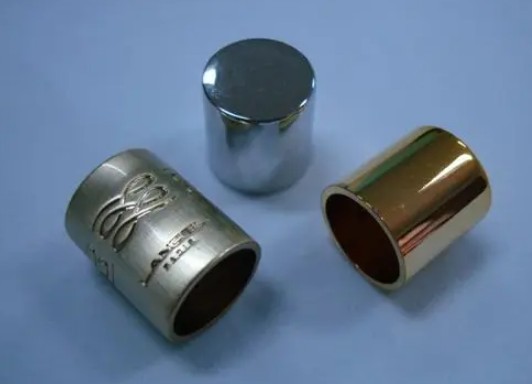
What is Porosity in Aluminum Die Casting?
Porosity refers to the presence of small voids or air pockets in the material after casting. In Aluminum Die Casting, porosity can occur due to trapped gases, improper cooling, or shrinkage during solidification. There are two main types of porosity:
- Gas Porosity: This is caused by gas entrapment, usually due to air or hydrogen being absorbed by the molten aluminum.
- Shrinkage Porosity: This occurs when the metal contracts unevenly during solidification, creating small voids inside the casting.
Both forms of porosity can lead to issues such as weakened mechanical strength, poor surface finish, and reduced lifespan of die-cast parts. For buyers relying on Aluminum Die Casting services, porosity is a major quality concern.
Why Preventing Porosity is Critical for Buyers
For businesses that depend on high-quality Aluminum Die Casting services, preventing porosity is essential to ensure the reliability and longevity of the parts they purchase. Here’s why porosity prevention matters:
- Quality Assurance: Porosity can lead to weak spots in die-cast products, reducing their structural integrity. This is particularly critical in industries like automotive and aerospace, where component failure can have serious consequences.
- Cost Implications: Porosity leads to increased production costs as defective parts must be scrapped or reworked. Buyers of aluminum die-cast products should look for suppliers who prioritize porosity control to avoid costly defects.
- Buyer Concerns: When selecting a Die Casting factory, buyers should inquire about the measures in place to prevent porosity. A factory that implements advanced porosity prevention techniques is more likely to deliver high-quality, reliable products.
Top Techniques to Prevent Porosity in Aluminum Die Casting
1. Optimizing Mold Design
A well-designed mold is essential to minimize porosity. In Aluminum Die Casting, the mold should be designed with optimal gating, venting, and runner systems. These elements control how molten aluminum flows into the mold and how gases escape, reducing the chances of gas porosity.
A Die Casting factory with expertise in mold design can help buyers avoid common porosity issues. By ensuring proper venting and using designs that promote even cooling, the risk of shrinkage porosity can also be minimized.
2. Controlling Metal Temperature and Pouring Rate
Maintaining the correct temperature during casting is crucial to preventing porosity. When molten aluminum is too hot, it can absorb more gases, increasing the likelihood of gas porosity. On the other hand, if the metal is too cold, shrinkage porosity may occur due to uneven cooling.
The Aluminum Die Casting service provider should control both the metal temperature and pouring rate to ensure optimal casting conditions. Slow and steady pouring minimizes turbulence, reducing air entrapment in the metal.
3. Vacuum-Assisted Casting
One of the most effective ways to prevent gas porosity is by using vacuum-assisted casting. This technique involves applying a vacuum to the mold cavity during the casting process, which helps remove trapped gases before the molten metal solidifies.
Vacuum casting is an advanced method that not all Die Casting factories offer, but for buyers seeking premium-quality aluminum die-cast parts, it’s worth considering. This technique ensures a higher level of quality by significantly reducing the chances of gas-related defects.
4. Proper Degassing
Hydrogen is the primary gas responsible for gas porosity in aluminum. Effective degassing is a critical step in Aluminum Die Casting to remove hydrogen from the molten aluminum before it’s poured into the mold.
Techniques like rotary degassing introduce an inert gas (e.g., argon or nitrogen) into the molten aluminum to force the hydrogen to escape. Buyers should ensure that the Aluminum Die Casting service they choose implements proper degassing methods, as this will directly affect the porosity level of the final product.
5. Using High-Quality Aluminum Alloys
The quality of the aluminum alloy used in casting has a significant impact on porosity. High-purity alloys are less likely to contain impurities that can lead to gas formation and shrinkage during casting. For buyers, selecting a Die Casting factory that uses premium materials is crucial to avoid porosity-related issues.
Premium Aluminum Die Casting services often include alloy selection and testing to ensure that the chosen materials meet the highest standards of quality, ensuring fewer defects and better performance.
6. Post-Casting Heat Treatment
Heat treatment is an effective way to reduce shrinkage porosity after the casting process is complete. This involves heating the die-cast part to specific temperatures and then cooling it in a controlled manner, allowing for the redistribution of material to fill any voids formed during solidification.
Buyers should look for Die Casting factories that offer post-casting heat treatment as part of their quality assurance processes. This extra step enhances the strength and reliability of aluminum die-cast products.
Quality Control Measures for Buyers to Look For
When sourcing aluminum die-cast parts, buyers should evaluate the quality control processes used by the Die Casting factory. Here are key measures to check:
- X-ray Inspection: This technique allows manufacturers to detect internal porosity in die-cast parts without damaging them. Buyers should ask if their supplier uses X-ray inspection to verify the quality of the casting.
- Pressure Testing: By subjecting die-cast parts to high pressure, manufacturers can check for hidden porosity that may affect the product’s performance in real-world conditions.
- Certifications: Look for factories that comply with international quality standards, such as ISO 9001, as these standards ensure that the factory follows rigorous quality control processes to minimize defects, including porosity.
Asking the right questions and understanding these key processes can help buyers choose a Die Casting factory that consistently delivers high-quality, porosity-free products.
Conclusion
Preventing porosity in Aluminum Die Casting is essential for delivering durable and reliable products. From optimizing mold design to using advanced techniques like vacuum casting and degassing, there are multiple ways to minimize porosity and ensure high-quality results.
For buyers looking for Aluminum Die Casting services, it is critical to select a Die Casting factory that implements these top techniques. By doing so, buyers can avoid the costly consequences of porosity, ensuring that their products meet the highest standards of performance and reliability.