Introduction
When it comes to manufacturing aluminum parts, selecting the right casting method is crucial for achieving quality, efficiency, and cost-effectiveness. Two of the most common methods are die casting and sand casting. Each technique has its unique advantages and disadvantages, making it essential for potential buyers to understand these differences before making a decision. This article aims to clarify the distinctions between die casting and sand casting, providing valuable insights for those looking to purchase aluminum die casting services.
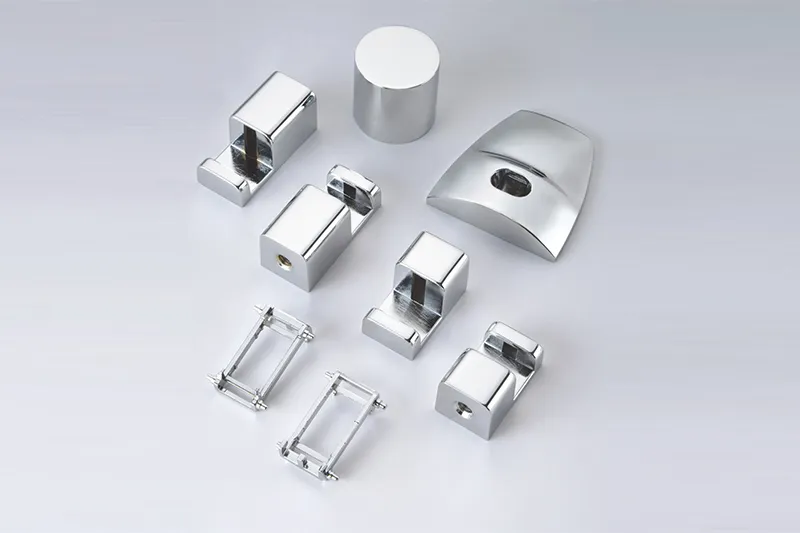
Overview of Die Casting
Die casting is a manufacturing process that involves forcing molten aluminum into a mold under high pressure. This method is particularly known for its ability to produce complex shapes with high dimensional accuracy and excellent surface finishes. There are two primary types of die casting: high-pressure die casting and low-pressure die casting.
- High-pressure die casting is the most common method, where molten metal is injected into a steel mold at high speeds, allowing for rapid production.
- Low-pressure die casting, on the other hand, uses lower pressure to fill the mold, which can be beneficial for larger components.
Die casting is widely used in industries such as automotive, aerospace, and consumer electronics due to its efficiency and precision.
Overview of Sand Casting
Sand casting is one of the oldest and most versatile casting methods. It involves creating a mold from sand mixed with a binding agent. The molten aluminum is poured into the sand mold to form the desired shape.
There are various types of sand used in this process, including:
- Green sand, which contains moisture and is often used for small-scale production.
- Resin-bonded sand, which provides better surface finishes and is suitable for more detailed work.
Sand casting is commonly employed in industries that require larger components or lower production volumes, such as construction machinery and art sculptures.
Key Differences Between Die Casting and Sand Casting
Production Speed
One of the most significant differences between die casting and sand casting is their production speed. Die casting allows for rapid cycle times, often producing hundreds or thousands of parts in a single day. In contrast, sand casting typically involves longer cycle times due to the manual processes involved in creating molds.
Dimensional Accuracy and Surface Finish
Die cast parts exhibit superior dimensional accuracy compared to sand cast parts. The high pressure used in die casting ensures that the molten aluminum fills every detail of the mold, resulting in tighter tolerances. Additionally, die cast components often have a smoother surface finish, reducing the need for extensive post-processing.
Material Utilization
Material efficiency is another critical factor to consider. Die casting generally has higher material utilization rates due to its precise molding process, which minimizes waste. Conversely, sand casting may generate more scrap material because of its less precise nature.
Cost Implications
When evaluating costs, it’s essential to consider both initial setup costs and long-term expenses. Die casting requires expensive tooling and molds, making it less economical for low-volume production runs. However, once set up, it becomes cost-effective for large-scale production due to its speed. Sand casting has lower initial costs since it requires less expensive patterns but may not be as cost-effective for high-volume production.
Design Flexibility
Design flexibility varies significantly between these two methods. Die casting excels at producing intricate designs with thin walls but may be limited by tooling constraints. Sand casting offers greater flexibility in design but often results in rougher finishes and less precise dimensions.
Pros and Cons of Each Method
Die Casting Advantages
- High production rates
- Superior surface finish
- Excellent dimensional accuracy
Die Casting Disadvantages
- Higher initial costs
- Limited alloy options
Sand Casting Advantages
- Flexibility in design
- Lower initial costs
- Suitable for larger parts
Sand Casting Disadvantages
- Slower production rates
- Rougher surface finishes
- Lower dimensional accuracy
Choosing the Right Method for Your Project
When deciding between die casting and sand casting, consider several factors:
- Production volume requirements: If you need large quantities of parts quickly, aluminum die casting may be your best option.
- Complexity of part design: For intricate designs requiring tight tolerances, die casting is preferable.
- Budget constraints: If your project has a limited budget or requires low-volume production, sand casting might be more suitable.
Conclusion
In summary, understanding the key differences between aluminum die casting and sand casting can significantly impact your manufacturing decisions. Each method has its unique strengths and weaknesses that cater to different project needs. For those looking to invest in aluminum die casting services, consulting with an experienced aluminum die casting supplier can provide tailored solutions that meet your specific requirements.
If you’re considering purchasing aluminum die cast products or services, take time to assess your project needs carefully before making a decision. By doing so, you can ensure that you select the most appropriate method for your manufacturing goals. Feel free to let me know when you would like me to continue!