Aluminum Die Casting Service
- One-Stop aluminum die casting solution provider
- 30+ years of experience, served 500+ Companies
- ISO 9001 & ISO 13485 & IATF 16949 certified
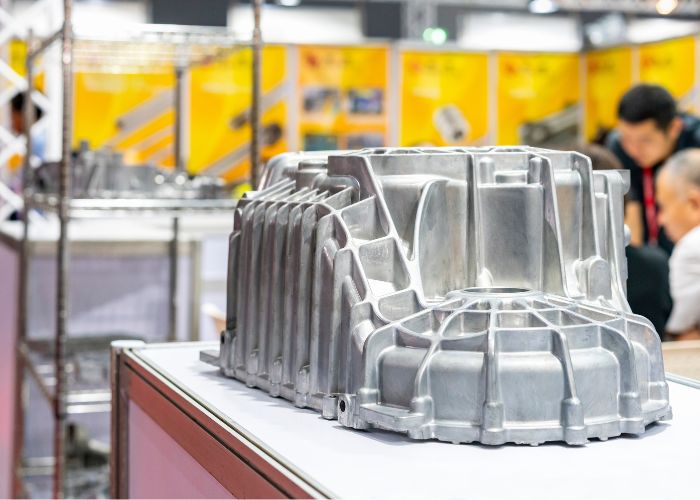
One-stop Service Manufacturer from Mold Production to Die Casting to Machining to Surface Treatment
One-stop service manufacturer from mold production to die casting to machining to surface treatment

Start with Qualified Raw Materials
Aluminum alloy should be die casting in cold chamber die casting machine
1. Smaller density, high specific strength;
2. Good mechanical properties, especially the impact toughness is also very good;
3. Good thermal and electrical conductivity, good mechanical cutting performance;
4. Good wear and corrosion resistance;
5. Good die-casting properties, better surface roughness and less thermal cracking;
6. Large body shrinkage, easy to produce shrinkage holes;
7. Aluminum alloy and iron have strong affinity, easy to stick to the mold.
1, Aluminum alloy has better thermal conductivity, electrical conductivity, cutting performance;
2, Aluminum alloy line shrinkage is small, so it has good filling performance;
3, Aluminum alloy density is small, high strength, its tensile strength and density ratio of 9 ~ 15, in high or low temperature work, the same maintain good mechanical properties;
4. Aluminum alloy has good corrosion resistance and oxidation resistance, most of the aluminum alloy in fresh water, seawater, concentrated nitric acid, nitrate hydrochloric acid, gasoline and a variety of organic substances have good corrosion resistance.
Aluminum alloy can replace bronze for low, medium speed medium temperature heavy-duty bearings, the price is 50% lower than bronze bearings.
Can also be produced through continuous casting or centrifugal casting profiles used in the manufacture of tiles, bushings, etc..
Can also be used to make molds, widely used in the production of bearings, a variety of pipe fittings, pulleys and all kinds of impact and wear castings.
Die casting aluminum alloy has a wide range of applications, mainly used in automobiles, engineering and construction, electric power, electronics, computers, household appliances, hi-fi speakers, military ships, aviation, aerospace and other military fields.
1. Low hardness, and at the same time wear resistance is relatively poor;
2. In the solidification of volume contraction is relatively large, about 6.6%;
3. High coefficient of linear expansion;
4. Easy to stick to the mold, need to strictly control the iron content in the range of 0.8% -0.%;
5. Low melting point, the use of high temperature is limited.
The Basic Concept of Die Casting
Pressure casting (referred to as die casting) belongs to the category of special casting. It is in the ordinary casting technology based on the development of an advanced technology, has a long history. Die casting is a kind of molten state or semi-molten state of the metal poured into the die casting machine pressure room, under the action of high pressure, with very high speed filling in the die casting mold (die casting) cavity, and under high pressure to make the molten or semi-molten metal cooled and solidified molding and obtain the casting of the high efficiency, high efficiency of precision casting method.
Trimming and Deburring
Deburring Burrs in die casting need to be removed by burring knives, grinding and polishing.
The casting itself needs to be designed in the early stage of the sharp angle into a rounded angle of 0.5MM or more to avoid heat cracking.
In recent years, labor cost is increasing, many manufacturers use CNC multi-axis deburring to improve consistency and reduce labor intensity.
CNC Machining
Die castings that require precision require CNC machining to ensure that the mold shrinkage causes deviations.
Die castings that require precision require CNC machining to ensure that the mold shrinkage causes deviations.
CNC machining is mainly divided into CNC milling machine and CNC lathe.
All of the above rely on computer control to produce precision Chinese CNC and foreign CNC mainly in Germany and Japan cnc higher precision.
Aluminum Die Casting Surface Treatment Is Divided Into 7 Categories
1. Powder Spraying
The main process of aluminum die casting is powder coating, the main realization of salt spray needs more than 24-48-36-96 hours, part of the street lamps or high salt offshore oil platforms also need 500-1000 hours, communication equipment also need to be powder coated to withstand the outside environment of the sunshine and rain, there are some powder coated need to be passed through the food-grade to ensure that a lot of drinking quilt is also powder coated, powder coating is one of the most common surface treatment processes of aluminum die casting, and it is also one of the most common surface treatment processes in aluminum die casting. Powder coating is one of the most common surface treatment techniques for aluminum die-casting.
2. Paint spraying
Paint spraying is also used for aluminum die-casting parts, and many of them are also used in cameras, furniture type equipment, specifically, the better quality part needs paint spraying, the rest of the parts are not very different, paint spraying environmental wastewater is bigger.
3. Electrophoresis
Electrophoresis is the nature of spray paint, but their color is usually black or a standard amount of large colors with electroplating cylinders so that the paint can be quickly colored if the spray paint color is only some of the basic colors of black or silver gold watch color maybe electrophoresis a choice, if you need a special color need to open the cylinder, but if the amount is too small and infrequent use will cause the cylinder to wear and tear at least two times per month, each time at least two days of production.
4. Teflon
At present, aluminum die-casting is still used in pots and pans, and the subsequent surface treatment is Teflon, and the black pots and pans at home are Teflon color.
5. passivation
Passivation surface treatment is mainly used in new energy vehicle charging devices, internal components or mainly to increase the salt spray test time.
This process can also reduce the environmental pollution, if the internal components do not have much appearance requirements can be used passivation process, and reduce the impact on the environment, this process has long been used in Europe and the United States for many years.
6. Electroplating
Electroplating process in aluminum die casting, very few people use the main reason is the high defective rate, the vast majority of electroplating process in zinc alloy die casting used in decorative signage, sanitary ware, door knobs and so on.
7. Oxidization
Oxidation is one of the most controversial surface treatment of aluminum die-casting, after IPHONE4, a large number of surface treatment is changed to aluminum oxidation, they use the technology is not aluminum die-casting are used 7 series of aviation aluminum through cnc milling out, the main reason is because of the aluminum die-casting material adc12 contains silicon, in the process of oxidation will produce the phenomenon of black, if the aluminum oxidation of the black or black-like there is no problem, but the gold, silver, red and other bright colors will produce blackening, and so on, it will produce blackening. Some people change the material to dm32 or use pure aluminum die casting, which also produce different degree of problems, change to dm32 simply put, replace the silicon into other materials so that although it is easy to die casting and oxidation, but the lack of silicon under the casting of sand holes will become more, the use of 6063 pure aluminum die casting will be easy to produce problems such as sticking to the mold and so on, all according to the shape to assess.
Aluminum Die Casting
Packaging and Transportation
Which kind of packaging is needed is mainly determined based on the volume of the casting.
If the casting is very small, it can be packed in an op bag through blister packaging or pearl cotton or paper packaging the outer box is usually a carton.
If the main item is large, it needs to be covered with foam because foam is enough to protect large items. Some customers will also put cartons on the outside and purchase pallets separately for shipping abroad.
Generally speaking, international trade is mostly FOB and EXW.
Generally, we will communicate in advance how to ship the goods.
Characteristics of Aluminum Alloy Die Casting
The main characteristics of aluminum alloy die-casting are as follows
Good casting performance
Aluminum alloy has good fluidity and can be molded into Various complex shapes with precise dimensions and good casting performance.
Low density and high specific strength
The density of aluminum alloy is approximately 2.5-2.9 grams /Between 3 centimeters, the specific strength (δ b>r) is relatively high.
Good corrosion resistance, wear resistance, thermal conductivity, and electrical conductivity
Aluminum alloy has good Good corrosion resistance, able to resist the erosion of most chemical reagents such as acids and alkalis. with Aluminum alloy also has good wear resistance, thermal conductivity, and electrical conductivity.
Other characteristics: Aluminum alloy is prone to sticking to molds and has poor cutting performance. aluminium alloy The volume shrinkage rate is relatively high, making it easy to produce shrinkage cavities. In addition, the hardness of aluminum alloy is relatively high Low, it is easy to scratch and damage the surface of the workpiece during loading, unloading, and handling. In the process of aluminum alloy die-casting, it is necessary to fully consider the above characteristics and adopt Corresponding process measures are taken to obtain high-quality castings.
Grades and applications of cast aluminum materials
Cast aluminum material is a kind of widely used casting material, with good mechanical properties, corrosion resistance and thermal conductivity, so it has been widely used in the industrial field. The following will introduce several common grades of cast aluminum materials and their applications.
A356.0
A356.0 is a low-iron aluminum alloy with good corrosion resistance and weldability. It is mainly used in the manufacture of automotive parts, aerospace parts and construction machinery. The A356.0 material has high strength and heat resistance and is suitable for various casting processes, such as die casting, sand casting and low pressure casting.
A380
A380 is a commonly used aluminum-silicon alloy with good rheological properties and corrosion resistance. It can be used to manufacture various mechanical parts, auto parts, electronic equipment enclosures and so on. The A380 cast aluminum material has good machinability, easy processing and assembly, and is widely used in machinery manufacturing, automotive and electronics industries.
7075
7075 is an ultra-high strength aluminum alloy with outstanding strength and corrosion resistance. It is widely used in the aerospace and defense industry, manufacturing aircraft parts, rocket engines and weapons equipment. 7075 cast aluminum material has good weldability, but the processability is poor, and usually requires heat treatment to improve strength and toughness.
ADC12
ADC12 is a common aluminum-silicon alloy, mainly composed of aluminum, silicon, copper, magnesium and other elements. It has excellent mechanical properties and corrosion resistance, and is easy to process. The ADC12 is widely used in the automotive industry for the production of automotive components, such as automotive engine covers, chassis components and body structures.
6061
6061 is an excellent cast aluminum alloy with high strength, heat treatment properties and corrosion resistance. It is suitable for manufacturing aerospace components, bicycle frames and ship structures. 6061 Cast aluminum material has good weldability and can be used to manufacture parts that need to be welded.
In summary, cast aluminum materials have good mechanical properties, corrosion resistance and thermal conductivity, and are widely used in automotive, aerospace, mechanical manufacturing, electronics and other fields. Different cast aluminum materials have different characteristics and applications, and selecting the right material according to specific needs can ensure the quality and performance of the product and improve production efficiency.
Aluminum Die Casting Processing Capabilities
Standard | Capabilities | ||||
Casting Size (mm) | 10-1000 | ||||
Maximum Casting Weight (kg) | 10 | ||||
Minimum Wall Thickness (mm) | 0.5 | ||||
Tolerance (mm) | 0.02 | ||||
Surface Finish | Ra1.6 | ||||
Tolerance | CT4-CT7 | ||||
MOQ | 500 | ||||
Additional Services | CNC machining, Powder coating, Anodizing, Assembly, Packaging, etc. |
Standard | Capabilities | ||||
Casting Size (mm) | 10-1000 | ||||
Maximum Casting Weight (kg) | 15 | ||||
Minimum Wall Thickness (mm) | 0.8 | ||||
Tolerance (mm) | 0.02 | ||||
Surface Finish | Ra3.2 | ||||
Tolerance | CT4-CT7 | ||||
MOQ | 500 | ||||
Additional Services | CNC machining, Powder coating, Anodizing, electroplating, painting spraing |
Surface Treatment of Aluminum die castings
Aluminum alloy die casting products, surface treatment is generally: powder spraying (i.e. powder spraying), paint, oil spraying, oxidation, sandblasting, electroplating and so on.
According to the thickness and finish of the surface treatment of the product
Powder spraying
Powder spraying is the use of powder spraying equipment (electrostatic spraying machine) to spray powder coating to the surface of the workpiece, under the action of static electricity, the powder will be uniformly adsorbed on the surface of the workpiece, forming a powdery coating.
The powder coating is cured by high temperature baking and leveling, and becomes the final coating with different effects (different kinds of effects of powder coatings);
The spray effect of powder spraying is superior to the spray painting process in mechanical strength, adhesion, corrosion resistance, aging resistance, etc., and the cost is also under the spray painting with the same effect.
Powder spraying, generally divided into outdoor powder and indoor powder.Grain can be adjusted to a variety of effects, such as smooth, sand, foam and so on.
Paint process
Paint process is to use aluminum alloy phosphating after spraying, spraying and then baking, such a coating is not only anticorrosive and bright wear-resistant, not easy to fall off Surface pretreatment
- Oil removal
- Water washing
- Rust removal
- Water washing
- able adjustment
- Water washing
- phosphating
- Water washing
- Water washing
- Drying
The purpose and importance of pre-treatment: the purpose of pre-treatment is to get a good coating, because the above stamping parts in the manufacturing, processing, handling,preservation period will have grease, oxide rust, dust, rust and corrosion on the surface, if not removed will directly affect the performance of the coating film, appearance, so the pre-treatment in the coating process occupies a very important position.
The significance of pre-treatment: pre-treatment, coating and drying are the three main processes of the coating process, of which the pre-treatment is the basic process, which has an important impact on the quality of the entire coating, the service life of the coating, the appearance of the coating, etc.
The workpiece surface is clean, uniform and grease free after degreasing, rust removal, phosphating and other processes
Oxidized
Aluminum alloy surface oxidation, suitable for conductive oxidation, aluminum or aluminum profiles, suitable for anodizing.
The oxidation color of aluminum alloy is generally natural, sky blue
Powder spraying, generally divided into outdoor powder and indoor powder.Grain can be adjusted to a variety of effects, such as smooth, sand, foam and so on.
1.Anodizing is carried out under the condition of high voltage electricity, which is an electrochemical reaction process;
Conductive oxidation does not require electricity, but only needs to soak in the liquid on the line, it is a pure chemical reaction.
1.Anodizing is carried out under the condition of high voltage electricity, which is an electrochemical reaction process;
Conductive oxidation does not require electricity, but only needs to soak in the liquid on the line, it is a pure chemical reaction.
2. Anodic oxidation takes a long time, often tens of minutes, while conductive oxidation only takes a short tens of seconds.
3. The film generated by anodic oxidation has several microns to dozens of microns, and is hard and wear-resistant, while the film generated by conductive oxidation is only about 0.01-0.15 microns.
The wear resistance is not very good, but it can conduct electricity and resist atmospheric corrosion, which is its advantage.
4. The oxide film is originally non-conductive, but because the film generated by conductive oxidation is really very thin, it is conductive.
Five, sandblasting on the surface of aluminum alloy products sprayed a layer of fine sand, enhance the friction coefficient of the contact surface, can enhance the reliability of the connection.
Sand thickness, grain is also very different.
Electroplating
Electroplating is the process of using electrolysis to deposit metal or alloy on the surface of the workpiece to form a uniform, dense and good bonding metal layer, which is called electroplating.
Simply understood, is a change or combination of physics and chemistry.
The application of electroplating process is generally used for the following purposes:
- Anti-corrosion
- Protective decoration
- Resistance to wear
Learn about Jiayuan Metal's die casting services
Jiayuan Hardware is good at aluminum alloy die casting and zinc alloy die casting: mainly through mold design and simulation to improve the mold flow path to reduce the air content of the product itself, through cnc control size or thicker gate, and diversified surface treatment at the back end: powder, spray painting, oxidation, electroplating, electrophoresis.
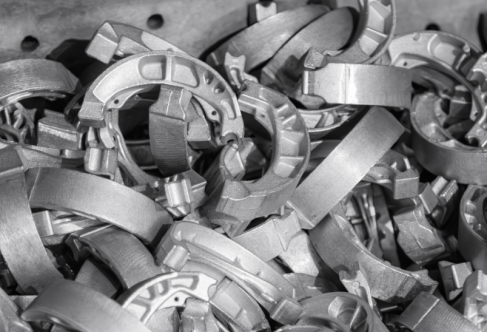
Frequently Asked Questions
Why is it so important to talk to customers about DFM?
What content is DFM need to inform in advance of possible bad and risk?
What is the common surface treatment and what may be suitable for the surface treatment?
What is the basic principle of die casting machine?
What there is a risk that the thinnest part of aluminum alloy can be achieved?
What are the causes of surface defects of aluminum alloy die-casting and how to improve them?