Communications Industry
Get high-quality manufacturing services for your custom Communications Industry prototypes and production parts. Launch products faster, reduce risks, and streamline production processes with on-demand production at competitive prices.
- Production-grade products
- ISO 9001:2015 certified
- 24/7 engineering support
Your Professional Communications Industry Molding Manufacturer
Communication 4G and 5G base station need aluminum alloy die casting, generally speaking, 400-1000-2000 tons of several sizes, large factories are responsible for the production of 1,000-2,000 tons of base station shells, there is no lack of many state-owned enterprises and listed companies in Shenzhen and Dongguan, generally speaking, the main problem in this regard is that the bigger the stuff they heat sinks the deeper the mold when the mold friction is very strong not good to take off the mold, and a lot of air in the mold! Mixing of air in the mold is difficult to discharge air, their mold design, there are a lot of secrets, the general small factories can not know and do not come out. After all, their technology is exclusive.
Why Choose JIAYUAN?
ISO certified
JIAYUAN is an ISO9001-2015 certified manufacturer that can guarantee top quality parts in an industry that demands rigorous consistency and quality control.
Huge production capacity
We can fulfill orders of virtually any size.
Range of services
As an equivalent parts shop and digital manufacturing expert, we provide CNC machining and manufacturing technology and services.
Easy quotation system
Our engineers will review your designs immediately to provide a fast and accurate quotation for the project.
Skilled and experienced
We have been manufacturing automotive parts for over a decade and our skilled engineers know how to get the best outcomes from your designs.
Short lead time
Our extensive facilities and partner network allows us to fulfill orders quickly, no matter the quantity or complexity.
What kind of Communications parts can we make?
Their factories are usually very large and divided into one level, two levels and three levels of suppliers, usually one level of suppliers have spraying and a lot of CNC, to ensure that part of the area can be conductive or some masking spraying is conducive to signal transmission, small die-casting to say that the base station is not difficult, and the amount of a lot of high speed rail a line that requires a lot of base station factories need to produce for a long time, each machine needs 3 sets of molds 24 hours a day to produce robotic spraying, a lot of times the amount of large will also do the die-casting. Sometimes the large volume will do die-casting island into a fully automated production line.
At present, the base station a lot of large numbers through the fully automated production mode, the amount of small is also through the semi-automatic mode of production depends on the situation, at present Huawei and ZTE are in Shenzhen and Dongguan production of similar shells after delivery to them, their factories have a similar large-scale production line to assemble shells, PCB boards, antennas, and other devices, may be the overall assembly and manufacturing is not difficult, the difficulty of research and development of the base station standard and the electronic chip and materials, is a huge system. It is a huge system project, die-casting is only the shell responsible for waterproofing, heat dissipation, placing PCB and device antenna and connecting cables, die-casting is the responsibility of the shell similar to the cell phone centerboard manufacturing.
The Communications industry requires all sorts of parts made from both metals and plastics. Typical priorities for Communications customers include:
- Tight tolerances for critical parts and assemblies
- Wear-resistant materials with certifications
- Excellent quality control via on-machine inspection and/or CMM
Communications Part Gallery
Below are some of the types of Communications parts we can manufacture for you:
- High speed router parts
- Smartphone device parts
- Optical module parts
- Electrical connector parts
- IC/LED precision parts
- Battery module connector
- Connector parts
- Information terminal connector parts
- Cloud server mechanical parts
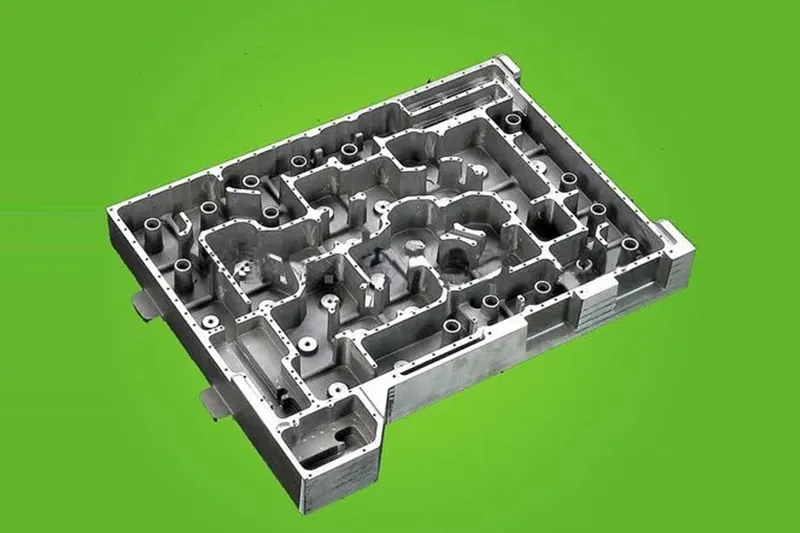
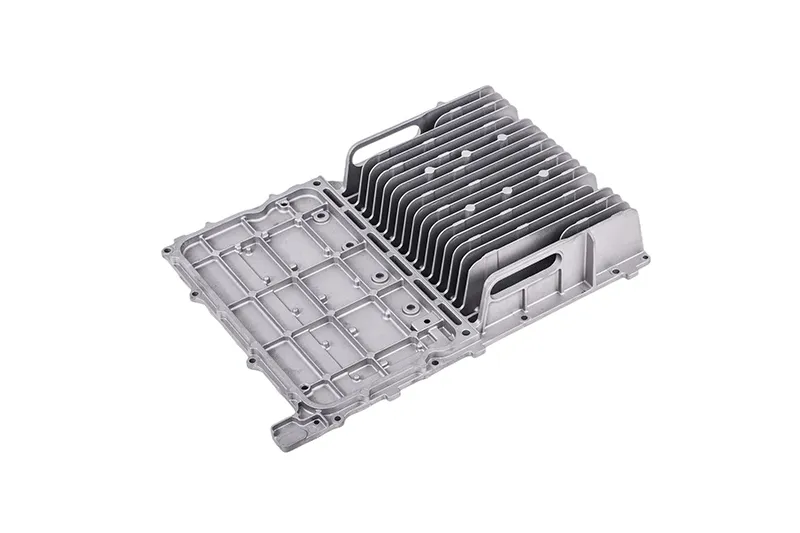

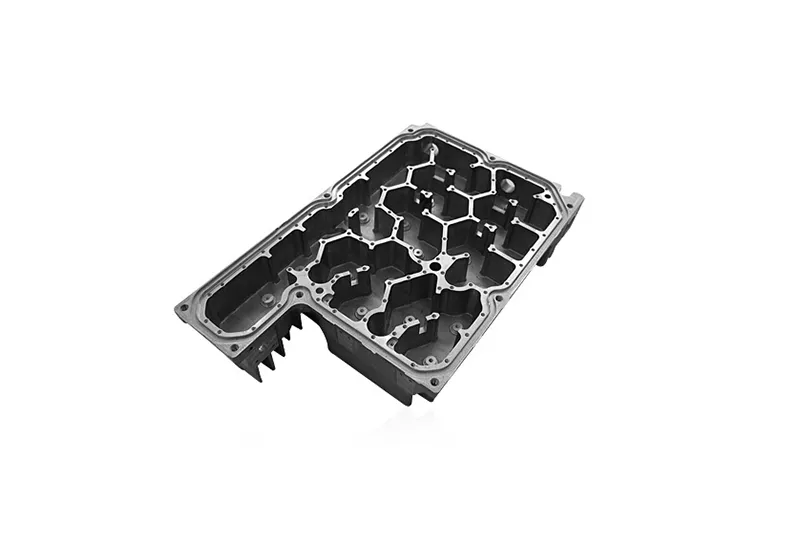
FAQ
First of all, customers need to send 3d, 2d drawings need to specify the material and precision requirements of our engineers can be carried out on the product molds and processing costs of the quotation. quotation usually takes 1 day because the main engineering and the boss on this side to review the quotation. Once the quote is confirmed, we can enter the engineering communication.
We provide a detailed DFM to ensure that subsequent problems can be minimized, firstly for thickness and chamfering corrections, then for mold pulling or structure that is not conducive to flow resulting in sand holes, skinning, cold segregation, as well as communication on the accuracy of the mounting position.
After confirming the DFM, we will start the molding process.
1:Drilling and tapping by milling machine or deep hole drilling.
2: CNC roughing
3: Hardening 46-48° (hardness depends on the size)
4: Fine milling to hit the right angle
5: CNC finishing
6: EDM discharge
7: CMM three-dimensional measurement (no three-dimensional can height ruler check)
8: Mold saving
9.Assembly
Temperature of the furnace → lifting the mold into the mold → locking the mold slot → locking the screw holes of the tie rods → connecting the oil pipe to the slider cylinder → adjusting the base action without error or interference → connecting the oil and water circuits → the temperature of the mold is determined → checking the PQ square diagram to adjust the pressure and punch speed
→Trial mold 100PCS→No obvious defects on the surface of the mold.
Scrape the cape burr→CNC processing→drilling and tapping→polishing and grinding→powder spraying surface treatment→sending samples to customers to confirm the samples→signing sample card→both sides confirm the sample board→conducting trial production→shipping to customers.